Recognizing What is Porosity in Welding: Reasons and Solutions
Porosity in Welding: Identifying Common Issues and Implementing Finest Practices for Avoidance
Porosity in welding is a pervasive concern that usually goes undetected up until it causes substantial troubles with the stability of welds. In this discussion, we will certainly check out the essential factors adding to porosity development, examine its detrimental results on weld performance, and discuss the ideal methods that can be adopted to decrease porosity incident in welding processes.
Usual Reasons For Porosity
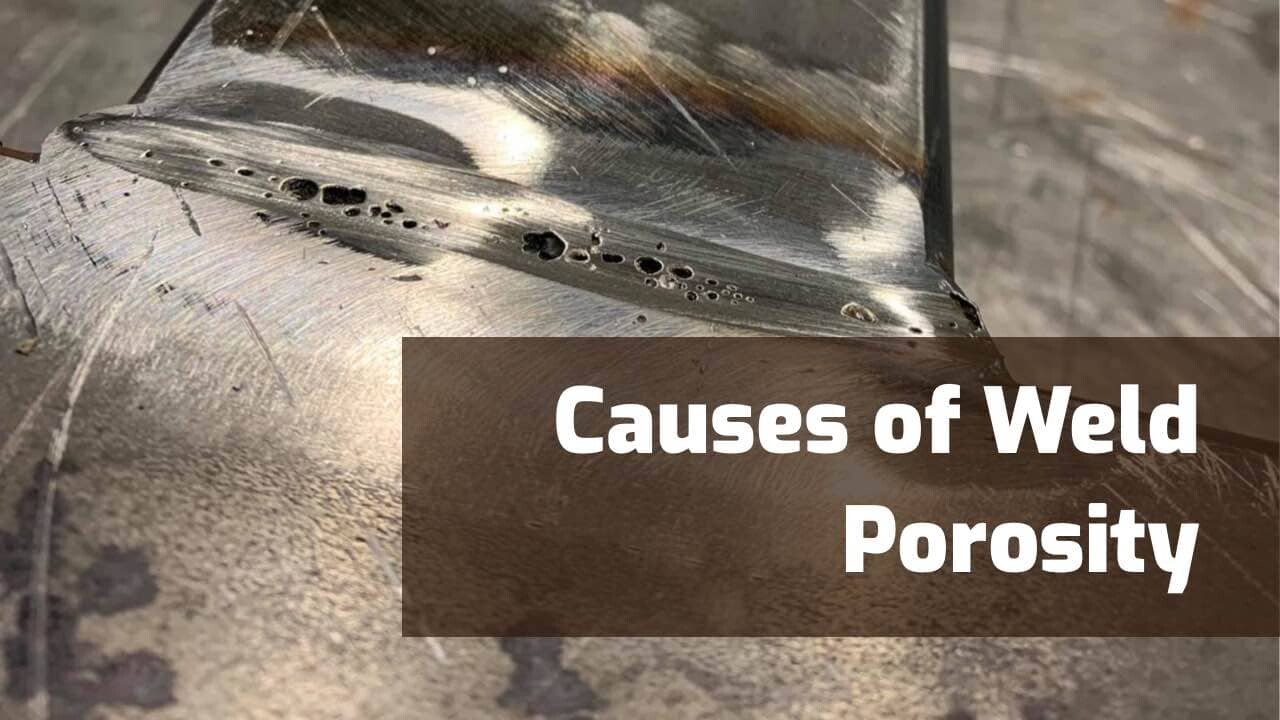
Utilizing unclean or wet filler products can present pollutants right into the weld, contributing to porosity problems. To mitigate these typical reasons of porosity, comprehensive cleansing of base steels, correct shielding gas selection, and adherence to ideal welding specifications are crucial practices in achieving high-grade, porosity-free welds.
Effect of Porosity on Weld High Quality

The visibility of porosity in welding can dramatically jeopardize the structural integrity and mechanical properties of bonded joints. Porosity develops spaces within the weld metal, compromising its general stamina and load-bearing capability.
One of the main consequences of porosity is a decline in the weld's ductility and durability. Welds with high porosity levels tend to show reduced impact toughness and lowered capability to deform plastically before fracturing. This can be especially worrying in applications where the welded parts are subjected to vibrant or cyclic loading problems. Additionally, porosity can impede the weld's capacity to efficiently transmit pressures, resulting in early weld failing and prospective safety and security threats in crucial structures.
Ideal Practices for Porosity Prevention
To enhance the structural integrity and top quality of bonded joints, what details actions can be applied to decrease the incident of porosity throughout the welding process? Using the right welding strategy for the specific material being welded, such as adjusting the welding angle and gun placement, can better protect against porosity. Routine assessment of welds and instant remediation of any kind of concerns determined during the welding procedure are crucial techniques to stop porosity and produce top quality welds.
Importance of Correct Welding Methods
Carrying out correct welding methods is paramount in making sure the structural stability and top quality of welded joints, developing upon the structure of efficient porosity avoidance measures. Extreme warmth click over here now can lead to boosted porosity due to the entrapment of gases in the weld pool. In addition, using the appropriate welding criteria, such as voltage, current, and take a trip speed, is vital for accomplishing sound welds with minimal porosity.
Furthermore, the selection of welding procedure, whether it be MIG, TIG, or stick welding, should line up with the details requirements of the job to make sure optimum results. Appropriate cleaning and prep work of the base metal, along with picking the right filler material, are likewise crucial components of skilled welding methods. By sticking to these ideal techniques, welders can reduce the danger of porosity development and create high-grade, structurally sound welds.
Testing and Quality Assurance Measures
Evaluating procedures are important to discover and avoid porosity in welding, guaranteeing the stamina and sturdiness of the final product. Non-destructive testing methods such as ultrasonic screening, radiographic screening, and aesthetic assessment are frequently utilized to determine potential defects like porosity.
Conducting pre-weld and post-weld examinations is additionally vital in maintaining quality assurance criteria. Pre-weld evaluations involve validating the materials, equipment setups, and tidiness of the workplace to stop contamination. Post-weld examinations, on the various other hand, assess the last weld for any type home of defects, consisting of porosity, and confirm that it fulfills specified criteria. Executing a comprehensive quality assurance plan that consists of comprehensive screening procedures and examinations is critical to reducing porosity problems and guaranteeing the total high quality of welded joints.
Conclusion
Finally, porosity in welding can be an usual issue that affects the top quality of welds. By identifying the common reasons for porosity and applying best methods for avoidance, such as proper welding methods and screening actions, see here now welders can make certain top quality and reputable welds. It is important to prioritize avoidance approaches to decrease the occurrence of porosity and maintain the integrity of welded structures.